GET INFORMED
Introduction to QRM by Rajan Suri
Rajan Suri is a professor of industrial engineering at the University of Wisconsin-Madison and an expert in production management. He’s especially known for developing the Quick Response Manufacturing (QRM) production management method.
Rajan Suri developed QRM in the 1990s in response to the inability of traditional production management methods to adapt to production requirements and demand in low-volume, high-variability production environments. Since then, QRM has been widely adopted by companies worldwide and has helped many companies improve their performance and competitiveness. The hundreds of companies include leaders such as Ford, Harley-Davidson and IBM.
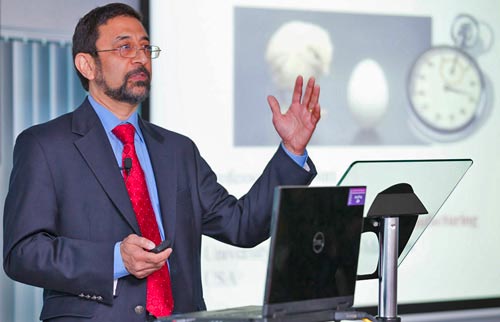
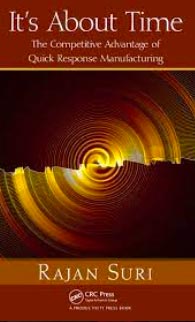
Presentation of the QRM Institute
The QRM Institute is a non-profit organisation that was created to promote the Quick Response Manufacturing (QRM) production management method, developed by Professor Rajan Suri.
The QRM Institute works in close collaboration with companies, universities and research institutes worldwide to support the implementation of this production management method. It offers training courses, certifications and consulting programmes to help companies incorporate QRM in their business culture and improve their performance.
The QRM Institute has also established the international QRM Standard. This standard provides guidelines for the implementation of QRM in companies and is used to assess companies’ maturity in this change process.
In addition, the QRM Institute is involved in research into QRM and publishes articles and case studies to promote the benefits of this production management method.
Why use 4.0 in my company?
The integration of 4.0 technologies can offer companies many advantages, including:
Improved PrODUCTIVITY
Automation, robotics and intelligent process control systems can increase the effectiveness of production processes, reduce downtime and increase production.
IMPROVED QUALITY
4.0 technologies enable real-time monitoring of product quality, which may reduce defects and improve overall quality.
REDUCED COSTS
Automation and robotics can reduce the labour costs, while real-time monitoring can reduce the costs associated with production defects.
IMPROVED FLEXIBILITY
Flexible production systems can adapt quickly to changes in demand and enable mass customisation.
INCREASED INNOVATION
Technologies can stimulate innovation by enabling faster and more precise design processes and by facilitating collaboration between in-house staff and suppliers.
REDUCED RISKS
Real-time monitoring systems can help prevent accidents and machine failures, thereby reducing the risks for employees and the costs involved in repairs.
Overall, integrating 4.0 technologies can help companies improve their efficiency, profitability and competitiveness on the market.
Presentation of the Interreg QRM 4.0 project
The Interreg QRM 4.0 project is a collaboration between several European countries which aims to promote the implementation of the Quick Response Manufacturing (QRM) method and 4.0 technologies. The project is funded by the European Union Interreg EMR programme
The project involves partners from two different European countries: Belgium (Flanders and Eastern Liège Province) and the Netherlands. Throughout the project, these partners worked together to share knowledge and best practices to promote the QRM method and 4.0 technologies in companies in the regions concerned.
There were multiple specific objectives of the Interreg QRM 4.0 project:
- Promote awareness and understanding of the benefits of QRM and 4.0 technologies among companies in the region;
- Provide training and support to help companies implement QRM and 4.0 technologies in their production processes;
- Establish networks and partnerships to facilitate collaboration and the exchange of knowledge between companies, universities, research centres and support organisations;
- Assess the project’s impact, the changes brought about by QRM and 4.0 technologies on companies’ performance and employment in the region.
The Interreg QRM 4.0 project is an example of European collaboration that supports innovation and companies’ competitiveness.
Information sessions
Throughout the project, information sessions were given on QRM 4.0 for companies to discuss their potential to improve companies’ competitiveness.
During the sessions, participants were able to learn more about the benefits of the QRM method, such as reduced production time, cost reductions, improved quality and flexibility and increased innovation. Participants were also able to discover how 4.0 technologies such as automation, robotics, the Internet of Things (IoT), augmented reality and artificial intelligence can be integrated to further improve production performances.
These sessions presented concrete examples of QRM and 4.0 technology implementation in similar countries, with demonstrable results of improved productivity and competitiveness. Participants also had the opportunity to interact with experts and project partners to ask questions and exchange ideas.
Overall, it was a valuable opportunity for companies to discover the potential benefits of QRM 4.0, to discover concrete examples of a successful implementation and to discuss their potential to improve their company’s production performances and competitiveness.
Four information sessions for SMEs were organised in different regions.
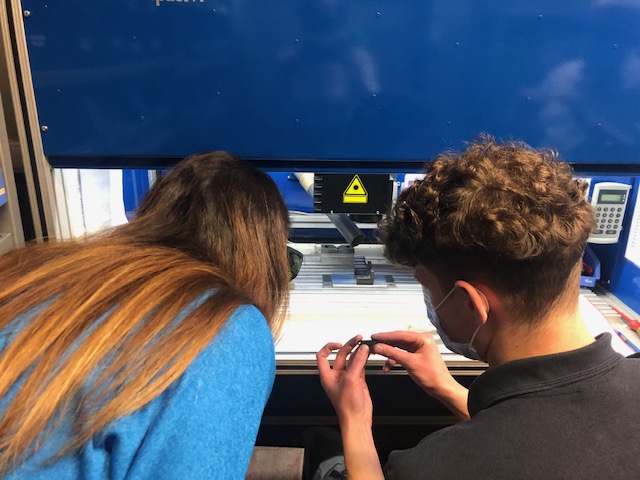
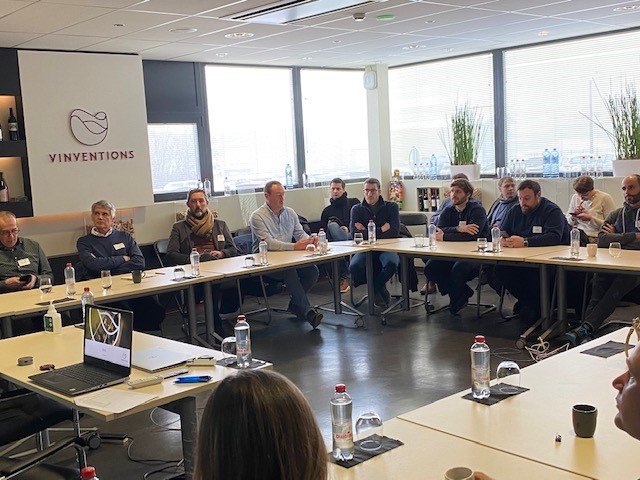
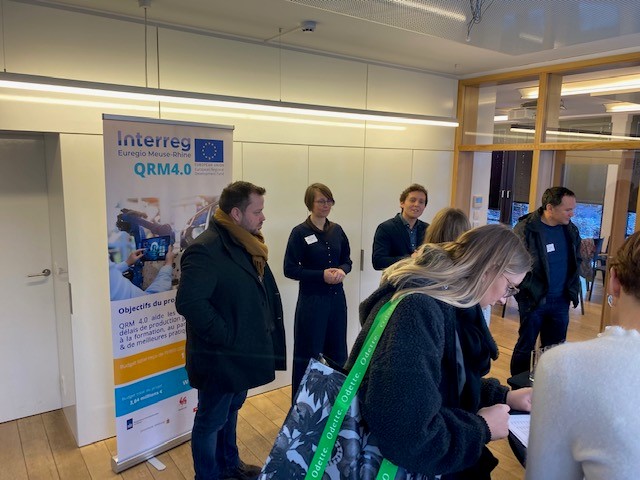
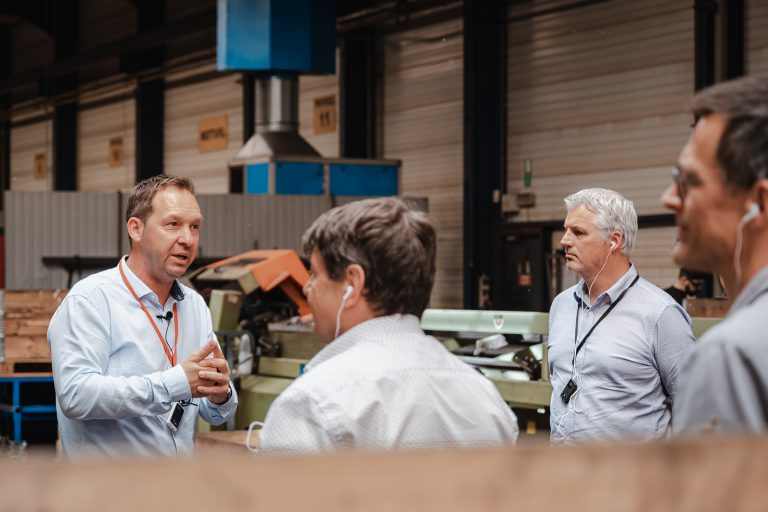
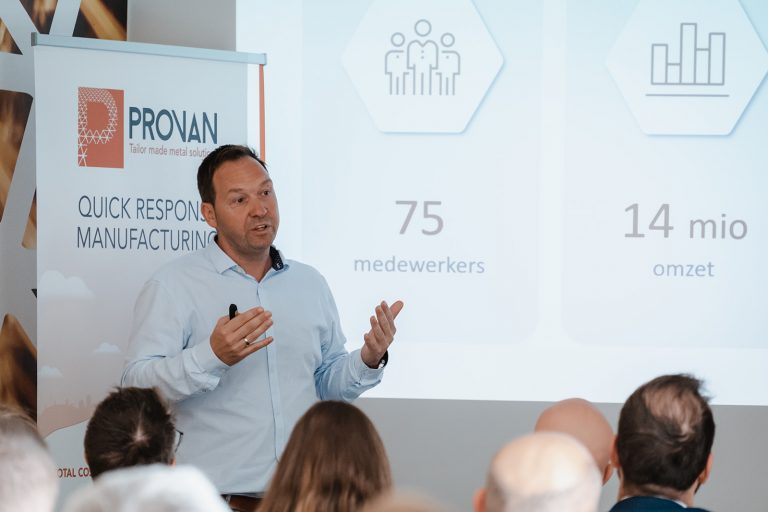
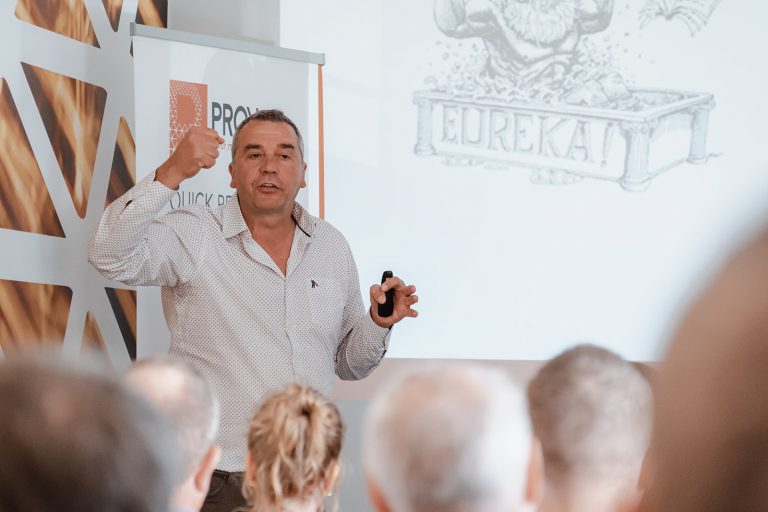
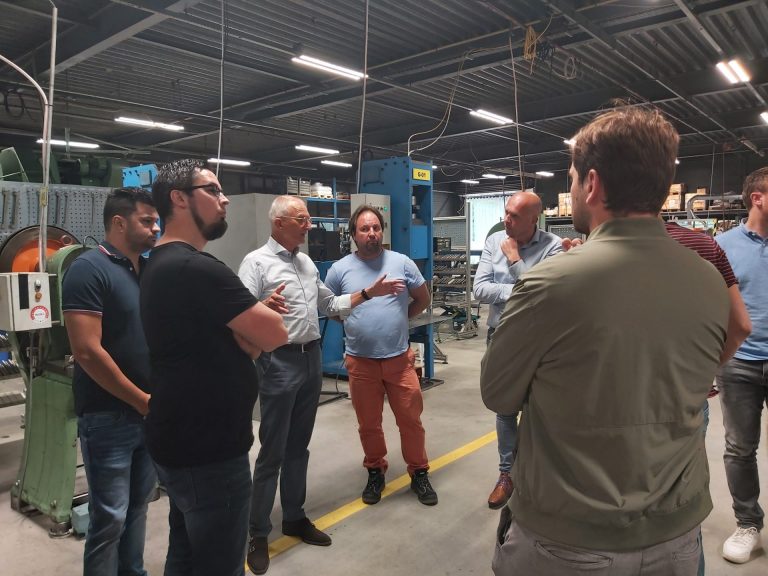
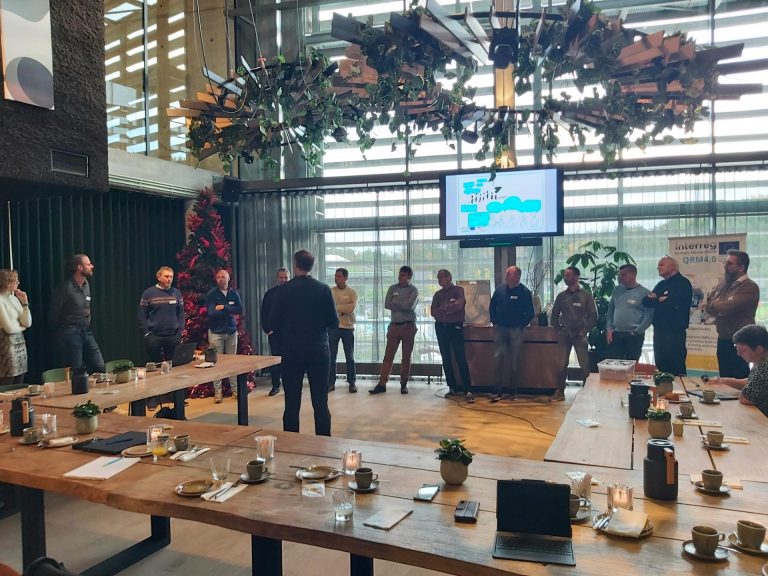
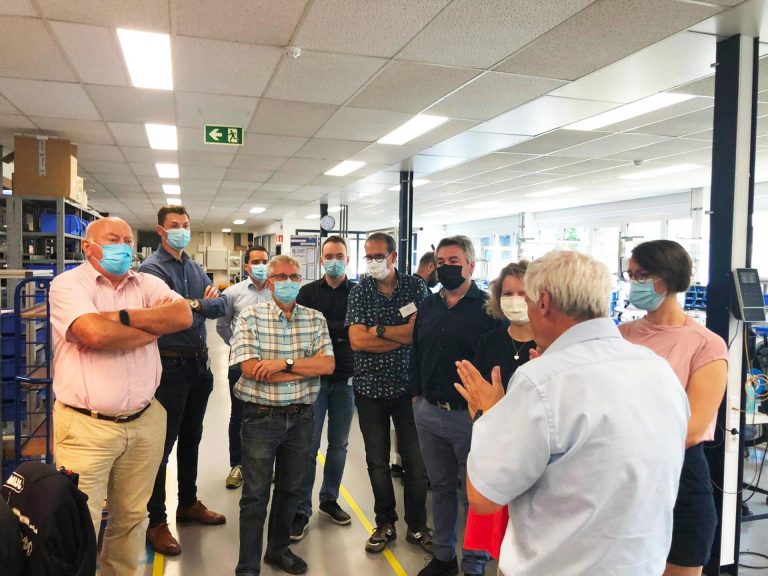
Testimonials
The company has implemented the Quick Response Quality Control method, which enables it to respond quickly to quality issues and identify targeted actions. The efficiency of this method means that Capaul can decompartmentalise its teams and refocus each employee on the company's priorities.
247TailorSteel helps their clients via QRM to speed up production processes. They themselves keep on evolving as well. Normally, clients had to wait a few days for the feedback whether parts were accepted or not. Now they can see right away if the parts are accepted after placing the quotation.
They will be informed right away through a short report in which the client can find possible solutions to adjust their drawings.
Fullwood Packo has learned a lot about implementing QRM in the past year. For example, it was found that there could never be enough communication with the parties involved. Aligning personnel with the QRM strategy is quite a challenge.