Train
What you need to know about QRM
Time as an ally
‘Thinking in terms of time’ is probably one of the most important principles of the QRM methodology. Processes are often analysed based on their costs. We all too often neglect ‘wasted’ time in all the steps of the manufacturing process.
Have you ever put yourself in an order’s shoes? Of all the time it takes this order to cross the company, what percentage of time does this order spend waiting to be taken care of?
E.g.
In this example, the company actually takes care of the order in 15 hours, or 2 calendar days (grey area) out of a total of 30 days. Therefore, the order spends 94% of the time in the company waiting; these are the white areas. The objective of QRM is to take action on these white areas and reduce them.
To be able to deliver within short and reliable time frames, it’s essential to change how you think. This means focusing on reducing white times, i.e. the waiting time between the different stages. It’s an important paradigm shift for companies and it requires a new vision.
The organisational structure
Many companies are organised into functional departments and, in practice, these departments turn out to be silos. And each silo is managed by a department head who does their best to organise their employees’ work.
But what’s often missing is communication between departments. People don’t talk to each other enough and this causes all kinds of problems.
This therefore means that we must first review the organisational structure and create the right structure that will enable people to collaborate better with one another.
In general, we must put people in smaller teams, focused on one market segment, QRM cells. This is an aspect of QRM. The company Provan is a great example: they put their first QRM cell in place in 2013.
Adapting system dynamics
This means understanding how interactions between machines, people, products and clients affect production lead times. This is connected to the variability of orders and the workload rate. Applying QRM stipulates that you can only plan 80% of a machine’s capacity. This means having 20% reserve capacity. This reserve is necessary to absorb contingencies and fluctuations in demand, with little impact on the lead time.
If you don’t have this reserve, then your work-in-progress will increase.
The whole company is concerned
The QRM method involves a cross-functional approach to reduce production times and product journey times. This requires all the company’s departments to work together to identify bottlenecks and blockage points in the production processes.
QRM involves the business culture being focused on collaboration and problem resolution. Including all the company’s departments in the change approach may help create such a culture by encouraging communication and collaboration between departments.
Planning in light of QRM 4.0
One question that companies always ask concerns planning. Companies often recruit scheduling managers, which is the position from which everything starts or depends on.
QRM shows that it’s more efficient to give operators independence. They will be more likely to accelerate decision-making, improve adaptability, take responsibility, solve problems more quickly and increase the company’s flexibility.
We have prepared a document to help you solve your planning issues.
QRM 4.0 learning network
The project’s partners have set up a learning network in each region. The objectives are to create a community of companies that are convinced by QRM 4.0, which continue to talk to each other after the end of the project, to learn from one another and to bring companies to the table that do not have the same level of maturity in terms of QRM 4.0.
In Liège Province, Basse-Meuse Développement organised five sessions over the course of one year. Three out of five sessions took place in a company and the participants discovered QRM through practical exercises.
The following companies have opened their doors to us and/or taken part in the network: Jumo, Issol, Paumelles Liégeoises, Val du Geer, Leyskens, les Ateliers Cerfontaine, Dumoulin Aero, PMT and Delhez.
In Flanders, several sessions were organised in the presence of SMEs from different sectors: Bioracer, Epower international, Lambrechts Nicolaers, Dings Kartonnages, Akarton, KS metaalwerken, KS metaalwerken, Strakk, Hugo consultancy, AIM BV and Seventwo.
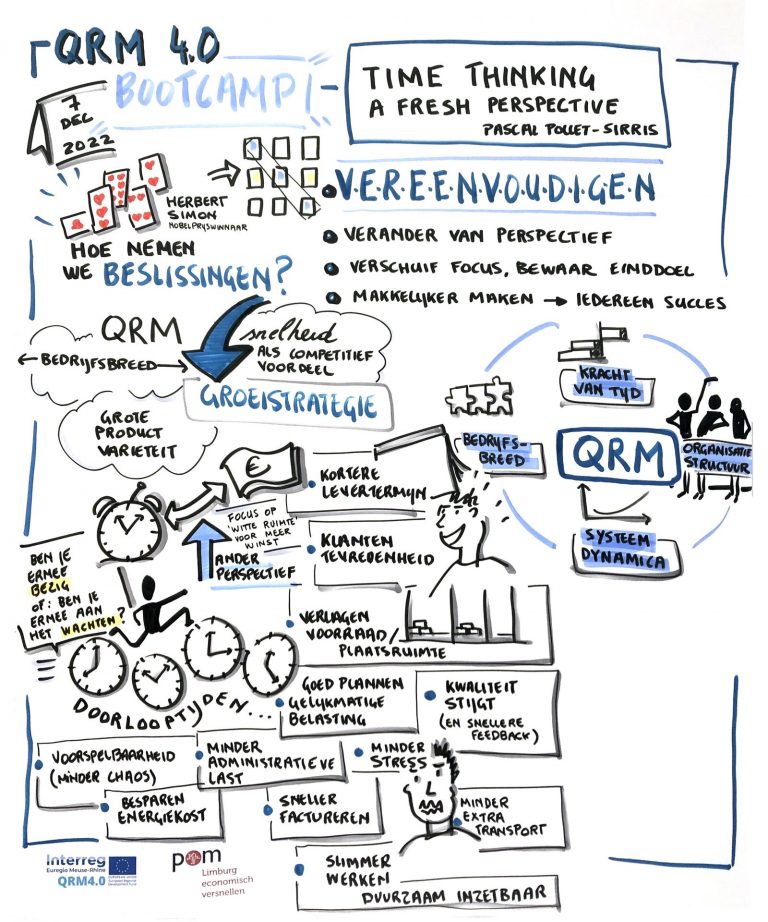
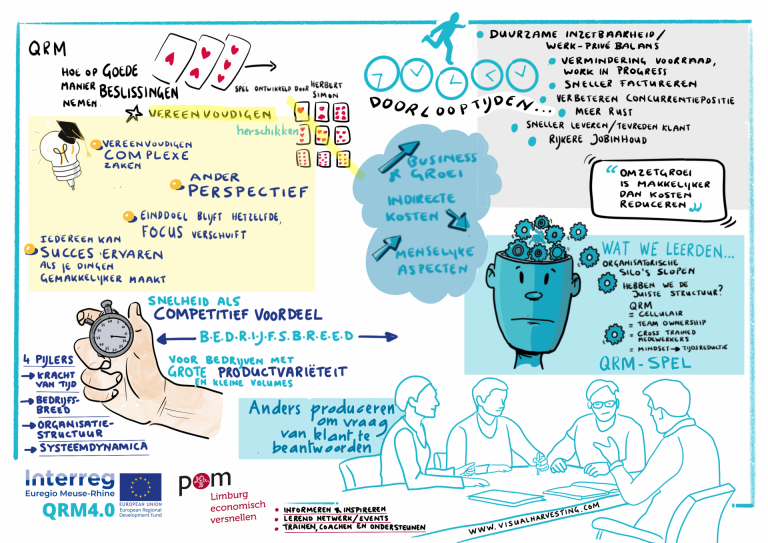
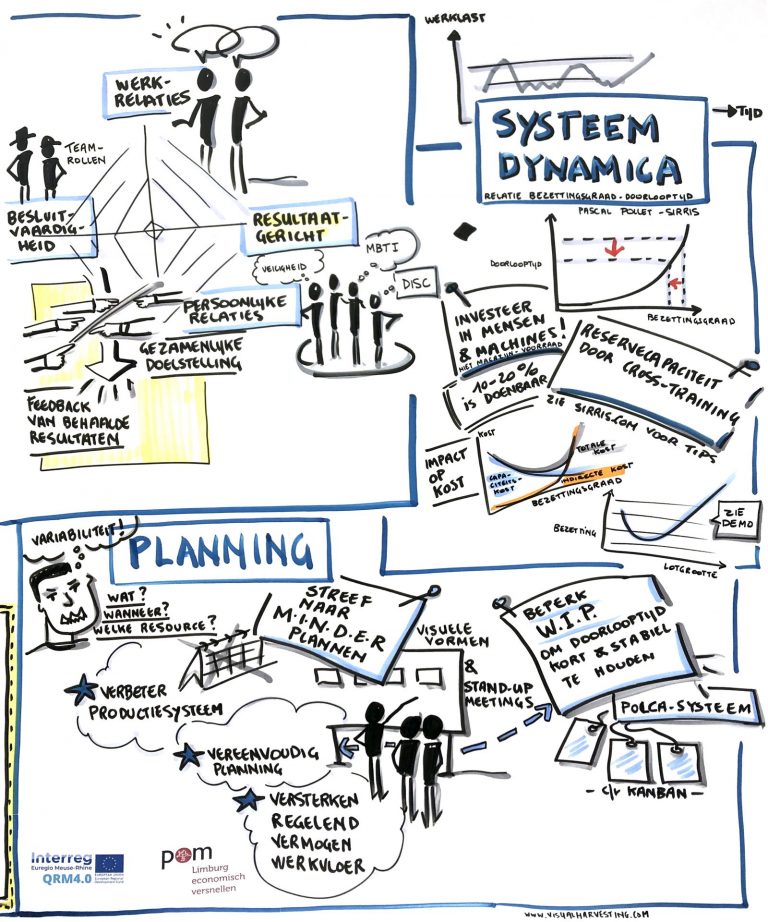
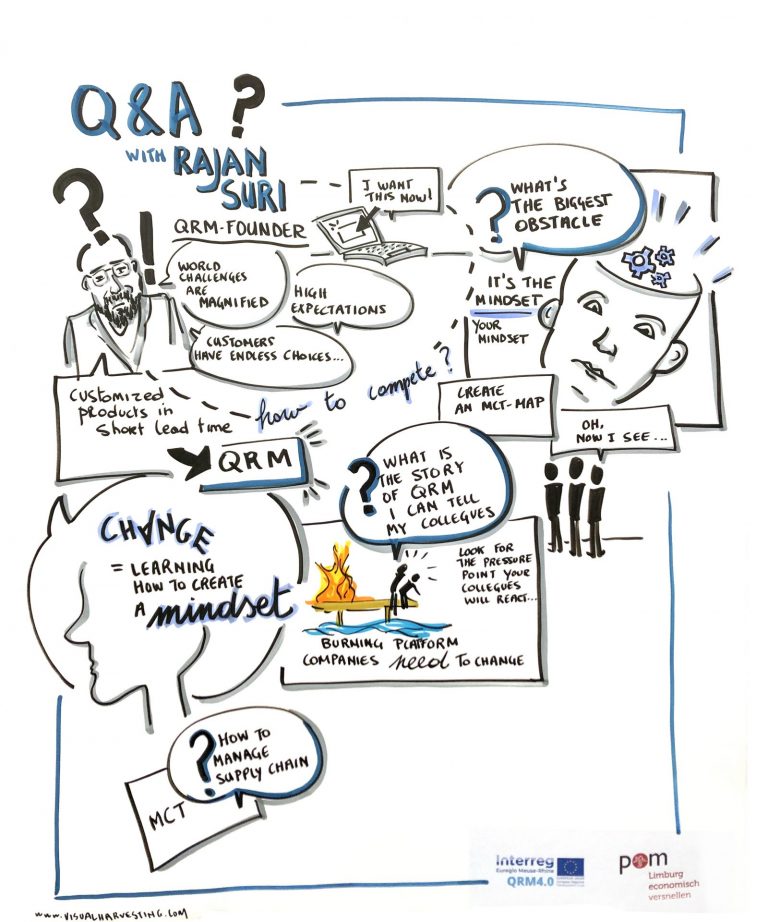
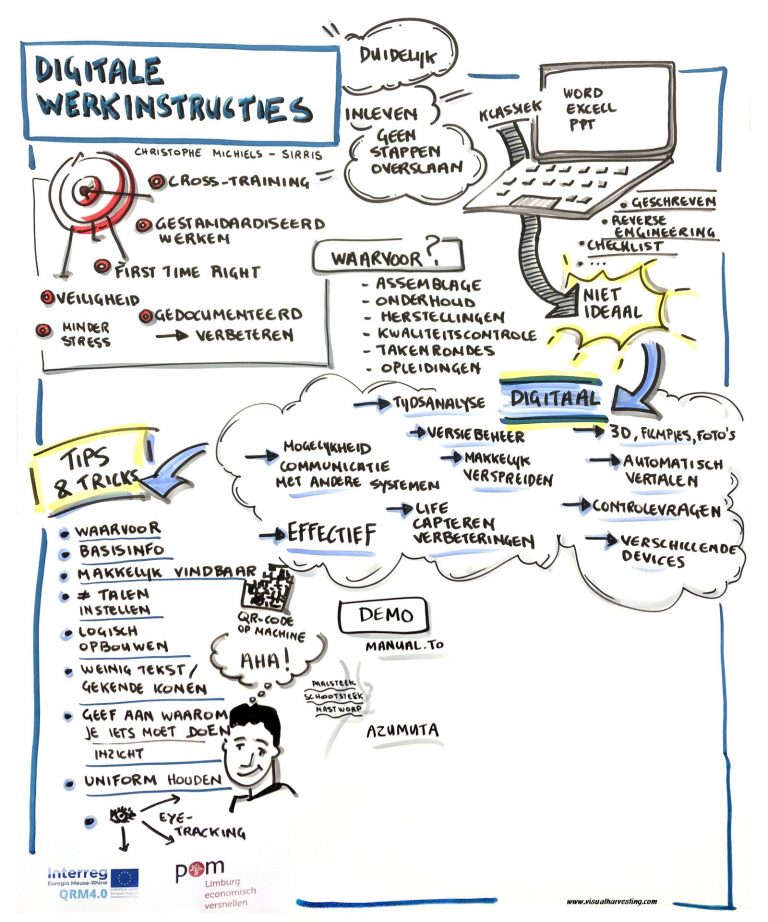
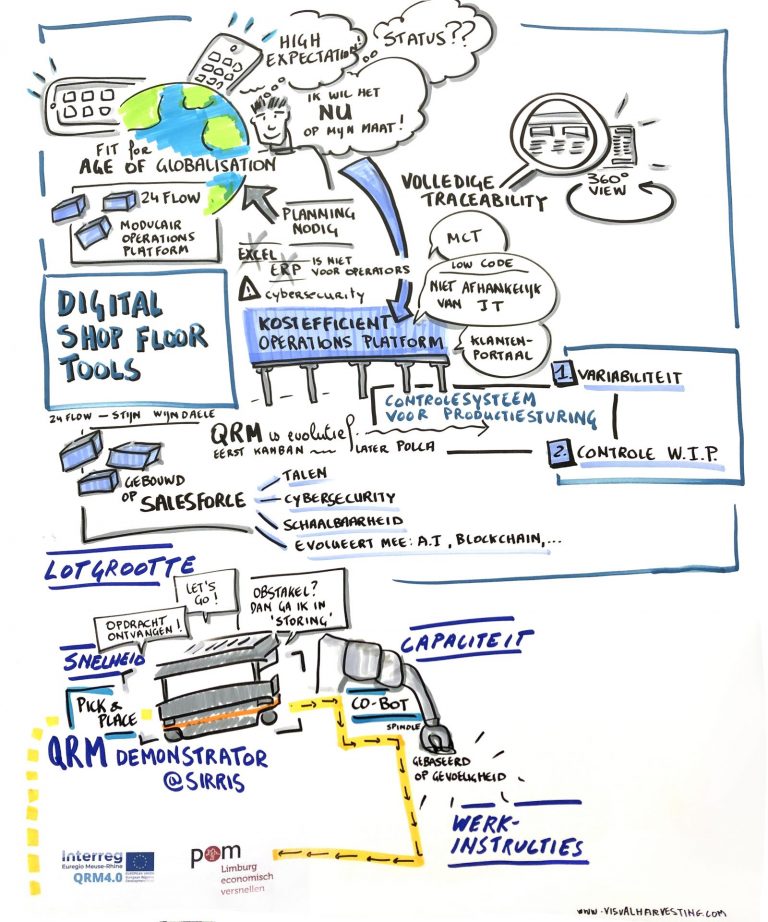
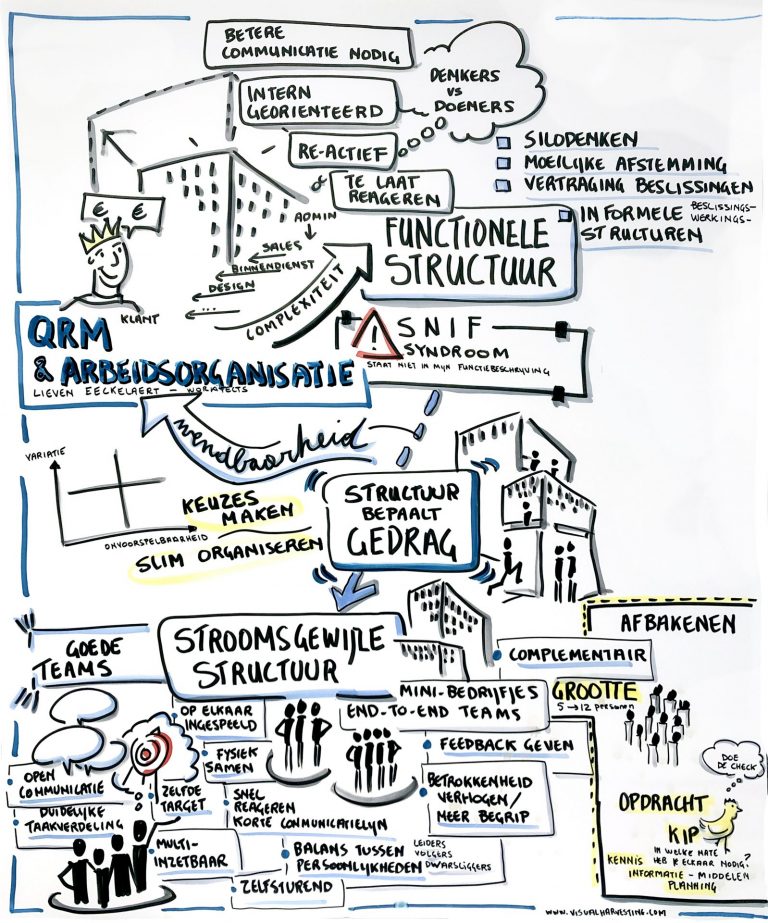
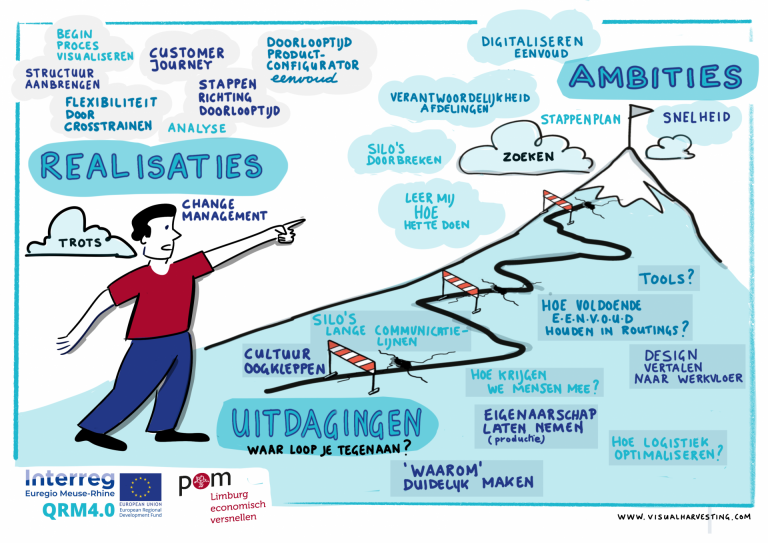
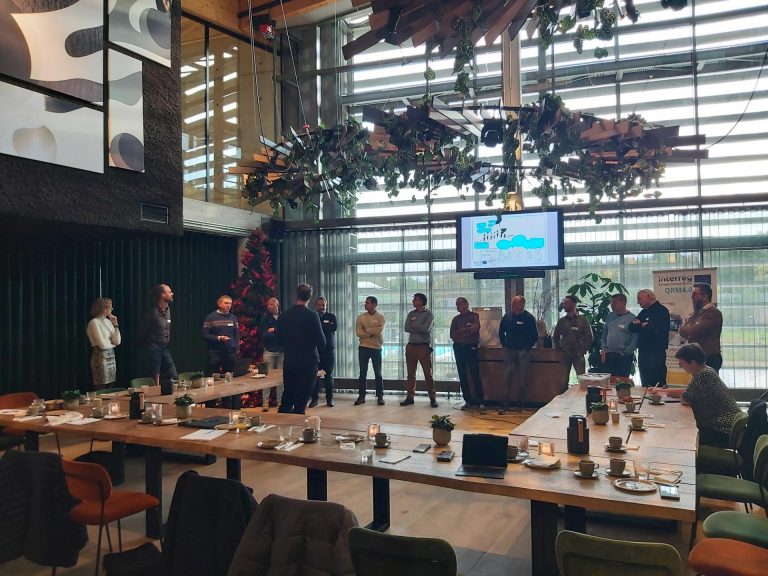
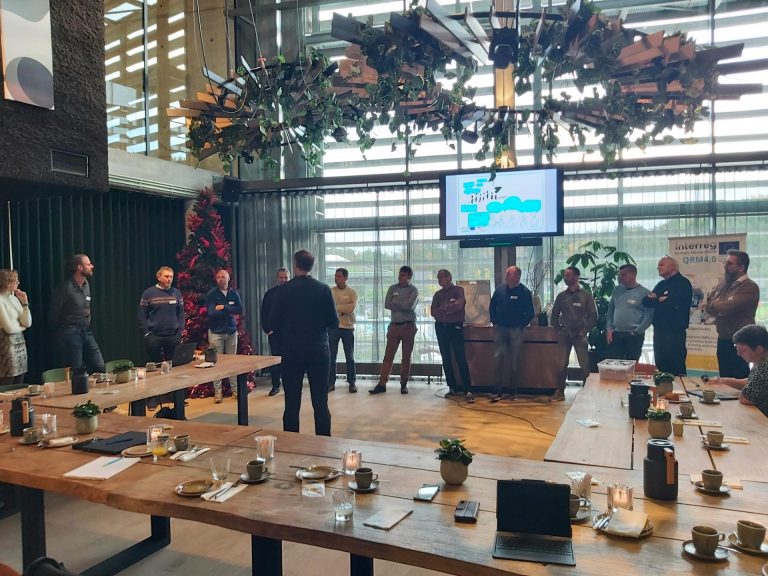
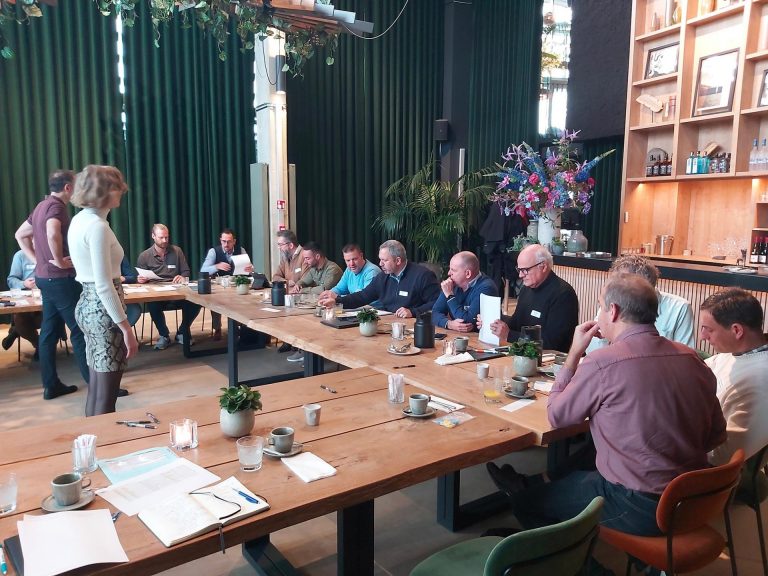
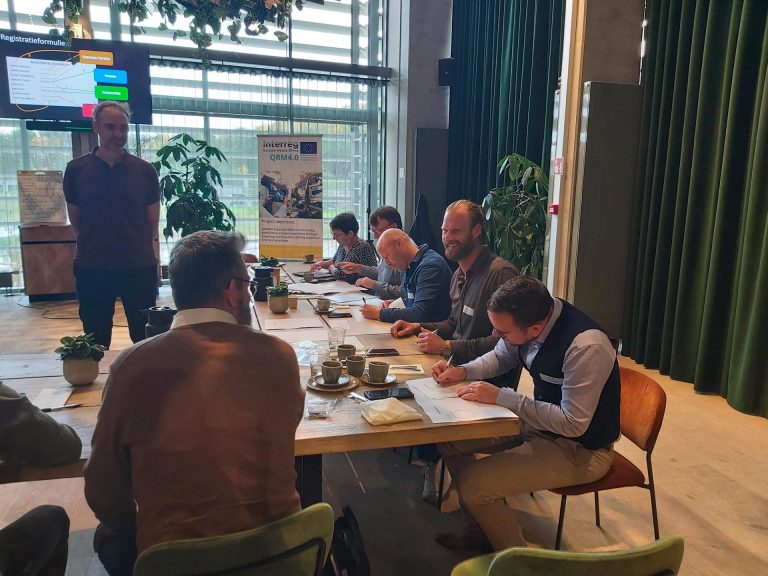
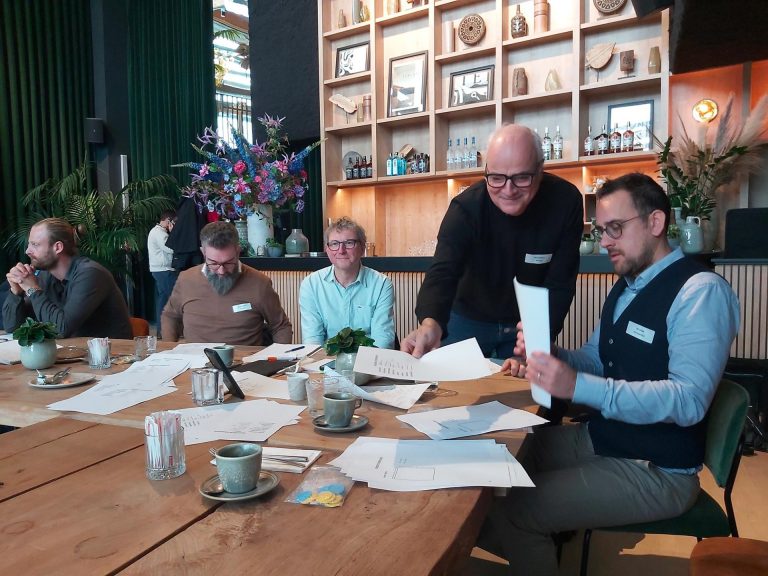
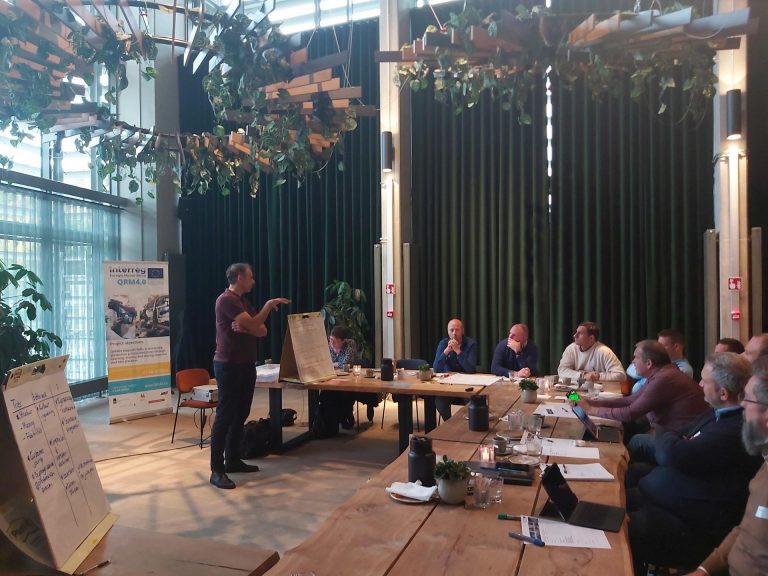
The Demonstrators
The relevant technologies
The QRM 4.0 project is the result of the collaboration between several partners. With regard to digital technologies, Zuyd Hogeshool is in charge of data analysis while Fontys works on connectivity and IoT platforms.
Sirris is in charge of the QRM aspect. Workitects takes care of the human aspect in the project. The technical operators are trained by Technifutur.
These different partners’ knowledge and expertise is provided in the form of practical technological data sheets. These data sheets can be downloaded free of charge and enable us to gain a better understanding of the potential and practical applicability of innovations focused on people combined with innovative digital technologies to reduce production lead times.
Overall, the QRM 4.0 project gathers experts in different fields to offer a comprehensive and innovative approach in terms of production process optimisation.
- Digital Work Instructions (EN)
- POLCA (EN)
- Application of the organizational canvas (EN)
- Causes of lead-time problems (EN)
- Do's and don'ts (EN)
- Digital story telling (EN)